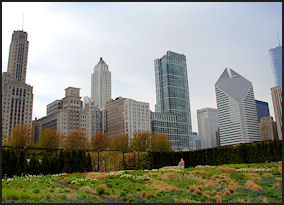
TQM gets you big buildings like this. Mad money, folks.
I understand there are different strokes for different folks. And when it comes to making up corporate minds about which management approach should be taken, you will not find one total path of agreement. There are so many options out there that it really boils down to either opinion or analytics. The latter is much more useful than the other, more often than not.
Now, we’d all like to have the objective approach and be able to pick which one works best, but the truth is that the infinite combinations of companies, products, markets, and global change don’t allow for one approach to be better for all applications.
You will eventually have to settle on the most effective approach when it comes to process improvement and a management approach that works for a lot of companies out there. Using Total Quality Management is an approach that should be strongly considered and I want to talk about the four main reasons this is true.
1) Plan: Define the problem
When a company decides to start out with a little bit of effort into planning where they want to go and get out of things, they’ll realize that the path has been defined and there’s actually something to work on now. It’s like the railroad tracks of a train. Without them in place, you can go everywhere. That may sound good, but it’s not. There’s only one place you should go and that’s to the next destination.
2) Do: Develop and implement solutions
This is where you take your plan, take the parts of it that make the most sense, and set up a path of what to get done. And then do it. This is to take the steps to where you want to go and to get to the next portion of your overall process. All thinking without any doing is just a bunch of wanna-be-do. It’s time to do-do here.
3) Check: Compare results
This is where you look back on the results that you have achieved and, if there are some type of objective measurements, you use those to refine your next iteration. You use those results to get to the next step in the process and to hopefully do away with any shortcomings along the way.
4) Act: A Results Feedback Loop
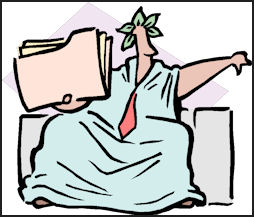
Back in the REAL empire days, a thumbs down was a good thing. Oh well.
After you’ve checked and compared your results to what you’ve obtained in the past, or for what you know to be average for your industry, you can start to see where you fit along the path. You can start to see how your return on investment matches up to the rest of your industry.
By using your results as feedback back into your iterative loops, you’ll begin to see which paths are not as optimal as others. And when you are able to find out what doesn’t work best, then you can reapply your people and your resources to that which makes the most sense for your company from an output perspective.
TQM is a Great Place to Be
Successful companies using Total Quality Management realize that they need to plan, that they need to implement those plans, that they need to check their results, and that they need to act on those results by using it as feedback into their iterative loop. Why don’t you have a friendly conversation with your Business Ops folks and see what they have in mind for your particular company.